Steam pipes are an essential component in many industrial processes, and they require proper insulation to ensure optimal efficiency and safety. Insulation is critical to prevent heat loss in steam pipes, which can result in energy waste and increased operational costs. In this article, we will discuss the importance of steam pipe insulation thickness and how to calculate heat loss for steam pipes.
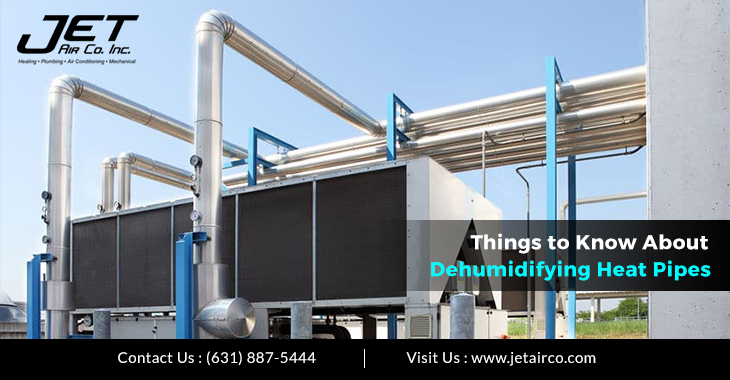
Steam Pipe Insulation Thickness
Steam pipes are typically made of carbon or stainless steel, and they operate at high temperatures and pressures. To minimize heat loss and protect workers from burns or other accidents, steam pipe insulation is necessary. Proper insulation can also prevent corrosion and condensation in pipes, which can damage surrounding equipment and infrastructure.
The insulation thickness of steam pipes depends on various factors such as pipe size, operating temperature, and environmental conditions. According to industry standards, the minimum insulation thickness for steam pipes is 2 inches, but thicker insulation may be necessary for larger pipes or higher temperatures. Isolation pads or insulation gaskets could help insulation, these items take-up the gap to close-in the distance and serves as a good alternative for leak-proof joints. Due to its flexibility, gaskets can adapt to a wide range of surfaces, making them the perfect solution to fill flange irregularities and provide the necessary sealing in any joint. These functions ensure that steam pipe insulation is effectively maintained and that heat and energy are transferred efficiently without leakage. Overall, thicker insulation leads to better efficiency in energy transference, saves money and reduces heat dissipation.
Calculating Heat Loss for Steam Pipes
The heat loss of steam pipes can be calculated using simple equations and thermal conductivity values. First, it is necessary to calculate the surface area of the pipe, which can be done using the pipe's diameter and length. The next step is to determine the effective thermal conductivity of the insulation material, which considers the conductivity of the insulation and the surrounding air. Lastly, the temperature difference between the steam inside the pipe and the ambient air outside the pipe must also be considered. The Q = U*A*(T1-T2) equation describes the overall heat loss computation where Q represents thermal power loss in a unit of time, U denotes the overall coefficient of heat transfer, A is the outer area of the insulation, T1 is the inside temperature, and T2 is the outside temperature.
Various software tools could be installed to detect the proper insulation thickness required for steam pipes. Pipe Insulation Thickness Calculation Software could automate the computation and analysis of pipe insulation thickness by considering the temperature, materials, humidity, and radius of the pipe thickness. This software saves time and resources by providing accurate data and reducing manual errors. Through monitoring and analytics, it becomes much simpler to know which parts require insulation along the pipeline, preventive maintenance is currently recommended.
In conclusion, steam pipe insulation thickness plays an essential role in reducing heat loss and promoting energy efficiency in steam systems. The thickness of the insulation requires proper understanding of the industry standards, and the calculation of the heat loss is a vital process to ensure proper insulation installation. In addition, leak prevention measures should also be taken via insulation gaskets or related equipment. Kingflex Insulation Co., Ltd. can provide high-quality insulation products and services to help optimize steam pipe insulation thickness and heat loss reduction. By utilizing software and professional guidance, industries could increase efficiency and minimize energy waste, ultimately reducing costs and promoting eco-friendliness.